A transformer rectifier is a compact and efficient device that combines two key functions in one unit: voltage transformation and AC to DC conversion. The transformer first steps up or steps down the incoming alternating current (AC) to the desired voltage level, and then the rectifier section converts this AC into direct current (DC). This setup is essential in applications where stable and controlled DC power is required, such as electroplating, electrolysis, anodizing, and cathodic protection systems. By integrating both components, transformer rectifiers offer improved efficiency, reduced space requirements, and easier maintenance—making them a preferred choice in many industrial processes that rely on consistent and reliable DC output.
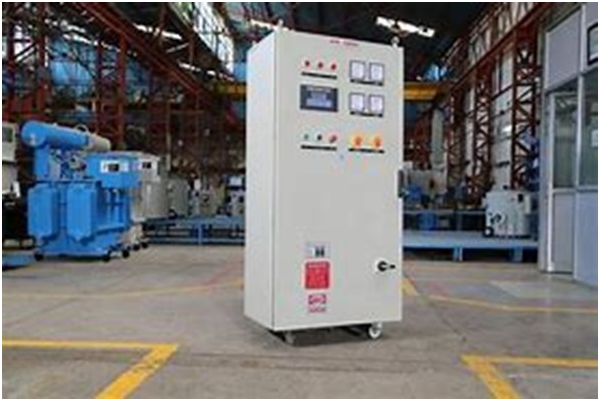
Transformer rectifiers are essential components in various industrial applications. They offer high efficiency and reliability in converting alternating current (AC) to direct current (DC). This guide provides a comprehensive overview of transformer rectifiers, highlighting their working principles, types, applications, and how they differ from conventional power transformers.
How a Transformer Rectifier Works?
A transformer rectifier converts AC to DC by first adjusting the AC voltage using a transformer and then rectifying it with diodes or thyristors. The transformer sets the appropriate voltage and provides isolation, while the rectifier ensures current flows in one direction to produce DC output. This setup is common in industrial applications like electroplating, battery charging, and electrostatic precipitation. Terms like “transformer rectifier unit (TRU)” and “rectifier transformer” vary by industry, all referring to devices that convert AC to stable, controlled DC power.
Key Components of a Transformer Rectifier
• Transformer: Step up or down the input AC voltage to the required level.• Rectifier: Converts AC to DC using diodes or thyristors.
• Cooling System: Prevents overheating during high-load operations.
• Control Panel: Manages output voltage, current, and protection settings.
Working Principle
1. Voltage Adjustment: The transformer modifies the incoming voltage based on the application requirements.2. Rectification: The rectifier circuit (typically a full-wave bridge) converts the adjusted AC into pulsating DC.
3. Filtration and Regulation: Filters smooth the DC output, and regulation systems maintain consistent voltage and current.
Types of Transformer Rectifiers
• Single-phase Rectifier Transformer: Suitable for light-duty applications.• Three-phase Rectifier Transformer: Common in industrial setups due to better efficiency and power handling.
• Oil-cooled vs. Air-cooled Units: Depending on environmental and usage conditions.
Industrial Applications of Transformer Rectifiers
Real-World Applications of Transformer Rectifiers
Transformer rectifiers play a critical role in pollution control systems, especially in electrostatic precipitators (ESPs) used in thermal power plants. A real-world example is highlighted in a 2025 case study by Yonder H2, which explores advanced transformer rectifier designs deployed in coal-fired power stations to improve particulate matter collection efficiency. These upgraded units use digitally controlled rectifiers with smart feedback systems, enabling more precise voltage regulation and reduced energy losses. Such innovations not only enhance air quality compliance but also improve operational efficiency in legacy plants. Read the full case study here
Transformer rectifiers are versatile and used in many sectors:
1. Electrostatic Precipitators (ESP)
• Used for particulate removal from exhaust gases in power plants.• It requires stable high-voltage DC power.
2. Electroplating and Anodizing
• Supplies DC for coating metals with a thin layer of another metal.3. Cathodic Protection Systems
• Protects pipelines, storage tanks, and offshore structures from corrosion.4. Smelting and Metal Refining
• Powers arc furnaces and electrolysis cells.5. Aviation and Aerospace
• Transformer Rectifier Units (TRUs) provide DC power to avionics and electrical systems.Feature | Transformer Rectifier | Power Transformer |
---|---|---|
Output Type | DC | AC |
Applications | Electrolysis, ESP, TRU | Transmission, distribution |
Rectification Included | Yes | No |
Control & Regulation | Often integrated | Basic voltage regulation |
Cooling Systems | Often more advanced (due to rectifier heat) | Less complex |
Design Considerations
When selecting or designing a transformer rectifier, engineers should consider the following:
• Load Requirements: Voltage, current, and power ratings.• Duty Cycle: Continuous or intermittent usage.
• Cooling Needs: Type of environment and required heat dissipation.
• Efficiency & Regulation: To ensure power quality and energy savings.
Market Growth and Industry Trends
The transformer rectifier market is experiencing steady growth, with projections indicating an increase from USD 0.508 billion in 2025 to USD 0.783 billion by 2033, reflecting a CAGR of 5.44%. This growth is driven by the rising demand for efficient power conversion systems across various industries, including aerospace, defense, and industrial automation. Notably, over 65% of aerospace and defense manufacturers have increased adoption of high-efficiency power conversion systems, boosting demand for transformer rectifiers.
Technological Advancements: IoT and Predictive Diagnostics
Modern transformer rectifier units (TRUs) are increasingly incorporating Internet of Things (IoT) capabilities and predictive diagnostics. Approximately 38% of newly launched TRUs now feature these advanced technologies, enabling real-time monitoring and proactive maintenance. Such innovations enhance operational efficiency, reduce downtime, and extend the lifespan of equipment, making them highly valuable in critical industrial applications.
Design Considerations: Cooling Methods and Customization
Designing transformer rectifiers requires careful consideration of cooling methods to ensure optimal performance and longevity. Depending on the application and environmental conditions, cooling can be achieved through air, oil, or water. For instance, oil-cooled units are preferred in high-load scenarios due to their superior heat dissipation capabilities, while air-cooled systems are suitable for environments where oil use is restricted. Customization of cooling solutions is essential to meet specific operational requirements and regulatory standards.
Emerging Applications and Future Outlook
Beyond traditional uses, transformer rectifiers are finding applications in emerging fields such as renewable energy systems and electric vehicle (EV) charging infrastructure. Their ability to provide stable DC power makes them integral to the efficient operation of solar inverters and fast-charging stations. As the global emphasis on sustainable energy solutions intensifies, the role of transformer rectifiers in supporting these technologies is poised to expand significantly.
Advancements in Transformer Rectifier Technology
Recent innovations focus on:
• Digital Controls: Offering remote monitoring and diagnostics.• Energy Efficiency: Reduced losses and improved cooling systems.
• Modular Designs: For easy maintenance and scalability.
Benefits of Using Transformer Rectifiers
• High Efficiency: Improved conversion from AC to DC.• Stable Output: Crucial for sensitive industrial processes.
• Durability: Designed to withstand harsh environments.
•Customization: Tailored to specific voltage and current needs.
Choosing the Right Supplier
Ensure your transformer rectifier is sourced from a reputable manufacturer that offers:
• Proven expertise in industrial power systems.• Customization options.
• Strong after-sales support and service.
Frequently Asked Questions (FAQs)
Q1: Can transformer rectifiers be used in residential settings?
A: No, they are typically designed for heavy-duty industrial applications.
Q2: What makes transformer rectifiers more efficient than separate systems?
A: Integrated design minimizes losses and improves Regulation.
Q3: Are TRUs and transformer rectifiers the same?
A: TRUs are a type of transformer rectifier used specifically in aviation.
Conclusion
Transformer rectifiers are pivotal in modern industry, powering processes that require reliable and stable DC output. Their applications are vast and critical, from electrostatic precipitators to aerospace systems. Businesses can make informed decisions and optimize their operations by understanding their design, functionality, and benefits.
If you plan to invest in industrial-grade transformer rectifiers, always consult an expert to choose the correct configuration and ensure long-term reliability.
Ready to upgrade your power systems?
Contact us today for expert advice and custom transformer rectifier solutions.